プロジェクト
ストーリー
Project
世界初(※1)、4ミクロンの壁を超えろ。
未知への挑戦が始まった。
2014年にリリースされた、旭ファイバーグラスのグラスウール断熱材『Aclearα(アクリアアルファ)』。世界初(※1)となる約3ミクロンの超細繊維が誕生するまでには、果てしないトライ&エラーを重ねる開発者(※2)たちの姿がありました。
※1 住宅用グラスウール断熱材(成形品)として。当社調べ、2014年7月1日発売時。
※2 開発者(Member)の所属・役職は、2023年3月21日時点のものとなります。
Member
-
Y.Y
生産本部 技術部
技術部長
1993年入社2007年の『Aclear』の立ち上げから手掛けてきた経験を活かし、グループリーダー(プロジェクト当時)としてプロジェクトチームをリードした。現在は生産本部の技術部長として、マネジメントや後進の育成に携わっている。
-
M.H
生産本部 技術部
グラスウールグループ
グループリーダー
2006年入社入社6年目~9年目にかけて『Aclearα』開発プロジェクトに携わる。同製品の発売後、グラスウール開発部門のグループリーダーとして当時培った知見を活かし、現在はAclearαを超える製品開発に引き続き取り組んでいる。
-
K.O
生産本部 技術部
生産技術グループ
主席
2010年入社入社翌年より『Aclearα』開発プロジェクトの主力メンバーに。新たな繊維化装置の開発などを担当。現在では「繊維化装置のことならOさんに聞け」と言われるほどのスペシャリストへと成長し、知見を活かしている。
-
T.T
生産本部 中部工場
製造グループ
2013年入社入社後、最初に配属されたのが『Aclearα』開発プロジェクト。新人のうちから知識を吸収し、その後は生産本部で同製品の生産性向上のための技術開発などに携わる。中部工場の立ち上げにも携わり、現在は同工場で活躍中。
STORY1
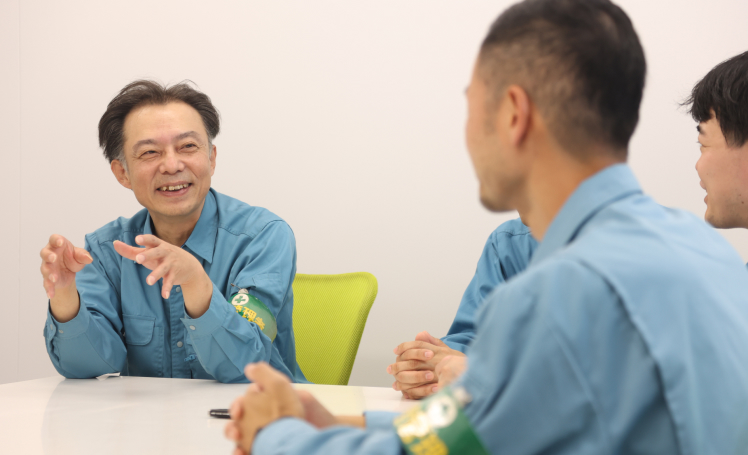
『4ミクロン』の延長線上に、
『3ミクロン』は存在しなかった。
カーボンニュートラル実現に向けた意識の高まりなどを受け、CO2排出削減に貢献するグラスウール断熱材には大きな期待が寄せられています。その可能性を追求すべく、未知の開発プロジェクトが立ち上がりました。
2007年、日本で初めてホルムアルデヒドを一切使わないグラスウール断熱材『Aclear(アクリア)』を開発した旭ファイバーグラス。2011年には4ミクロンという高性能グラスウールが市場を席巻するまでに成長を遂げていました。
そして2011年、新たな挑戦がスタートを切りました。世界にまだ存在しない『3ミクロンの超細繊維』による新製品の開発です。
当時、開発チームをまとめていたグループリーダー・(Y.Y)はこう振り返ります。「当初は、既存の技術をさらに追求していけば、3ミクロンにたどり着くと考えていました。でも、そうではなかった。3ミクロンは、4ミクロンの延長線上には存在しなかったのです」。
旭ファイバーグラスが有する世界最先端の製造設備をもってしても、4ミクロンの壁を超えることはできない――。約1年間の試行錯誤の末に開発チームが出した答は、開発コンセプトを抜本的に見直し、過去の成功事例に囚われず新たな発想で再スタートを切ることでした。
詳しい開発背景
2016年省エネルギー基準(仕様基準)において、北海道(1・2地域:寒冷地)では、壁・床に要求される性能は、熱抵抗値(R値) 3.3㎡・K/W。既存のグラスウール断熱材を使用してその基準を満たすためには、壁内への充填断熱に加え、壁外への付加断熱という二重断熱が必要です。ただし付加断熱の分、コストが跳ね上がり、壁が厚くなるため居住空間も狭くなります。従来通り壁内への充填断熱だけで基準を満たすためには、『3ミクロンの超細繊維』のグラスウール断熱材の開発が必要不可欠でした。
STORY2
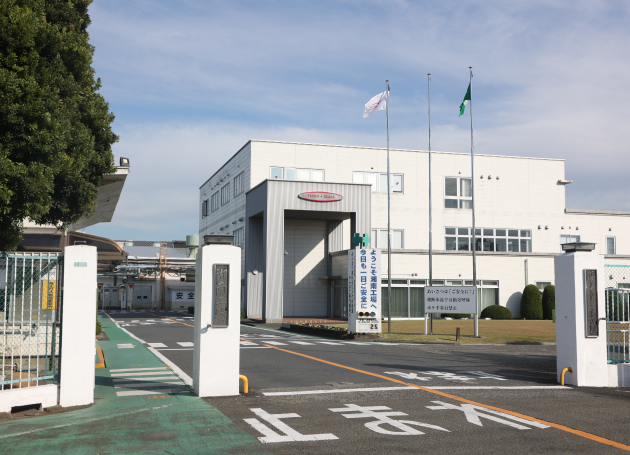
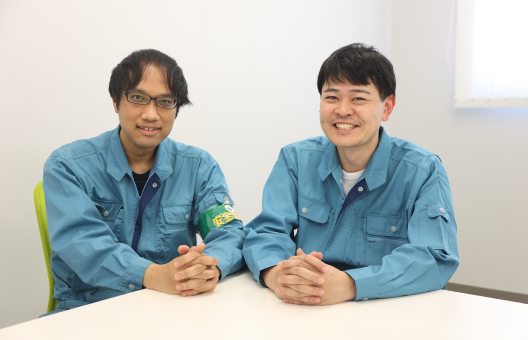
開発においてモノを言うのは、
経験や年齢ではない。
ブレイクスルーの鍵を握っていたのは、先入観を持たない20~30代の若手社員たち。彼らが主力となり、当初は可能性が低いと除外してきた開発アプローチについても徹底的に拾い上げ、検証を重ねていきました。
グラスウール断熱材が完成するまでには、いくつかの工程があります。
調合されたガラス原料を溶解窯に投入し、約1300℃という高温で溶かしていく。溶解したガラスを繊維化装置に流し込み、毎分数千回の速さで回転する特殊金属の回転体「スピナー」の遠心力を利用し、細い繊維状に加工する。その繊維を集め、約200℃のオーブンに入れ焼き固めて製品が完成する…というのが一連の流れです。
開発チームでは、当時入社4年目の(K.O)が中心となり、それらの工程を一つひとつ見直していきました。
「特に時間をかけたのは、スピナーの仕様の見直しです。スピナーの壁面には、流し込まれたガラスを細く射突する穴が空いているのですが、機械メーカーさんと相談しながら、穴の大きさや形などが異なる壁面をいくつも試作し、片っ端から検証していきました」(K.O)。
週1~2回ペースでテスト、レビュー、テスト、レビューを繰り返す日々。ついに3ミクロンの影が見えてきた時には、プロジェクトスタートから約2年が経過していました。
STORY3
成功未知数の新技術開発に挑戦。
ついに道筋が見えてきた。
3ミクロンの繊維そのものは実現しつつありましたが、製品化するためにはさらなる挑戦が必要でした。細い繊維は、ちぎれやすく、短くなりやすくなります。その繊維を「集める」という工程で新たな課題が発生したのです。
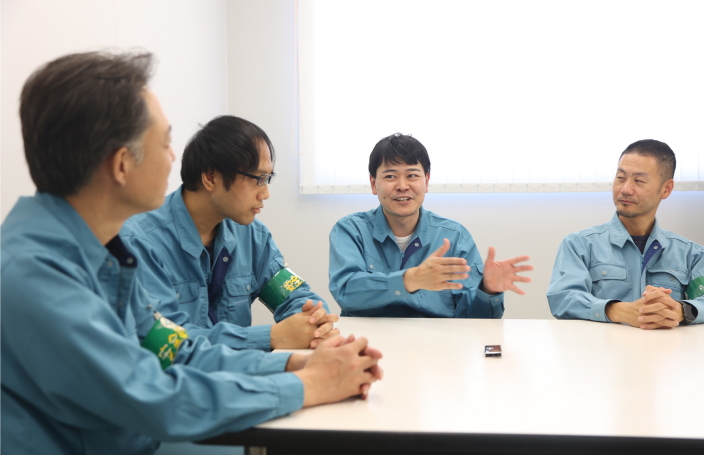
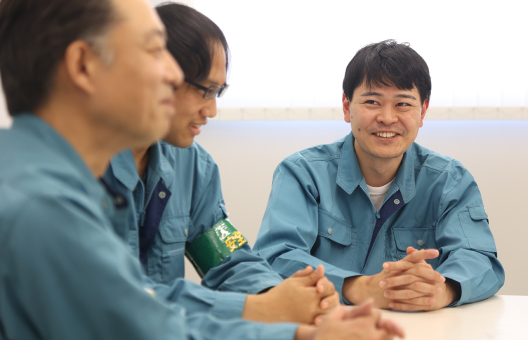
「完成した繊維は吸引して集めていくのですが、細く短い繊維はまとまりにくく、細くなることで通気抵抗も上がるため、既存の設備ではうまく集めることができませんでした。通気抵抗が上がるからこそ、断熱性能が上がっていくのですが…」(M.H)。
さらに、製品化するためには集めた繊維を「寝かせた」状態で板状にする必要があります。ですが、長さが短いと向きがバラバラになり「立ってしまう」繊維が出てきます。それでは立った繊維を通じて熱が伝わりやすくなったり、空気を通しやすくなったりするため、断熱性能の向上にはつながりません。
目指すは、細く、長い繊維。そして、それらを寝かせた状態で集める、新たな積層(せきそう)技術でした。
テストのために、小型の積層装置を試作することになったのです。「成功するかどうか未知数の技術開発でしたが、高級スポーツカーが買えるくらいの投資をして頂きました。その装置を小型の生産ラインに持ち込んでテストを繰り返し、2013年の後半、ようやく製品化までの道筋が見えてきたのです」(M.H)。
STORY4
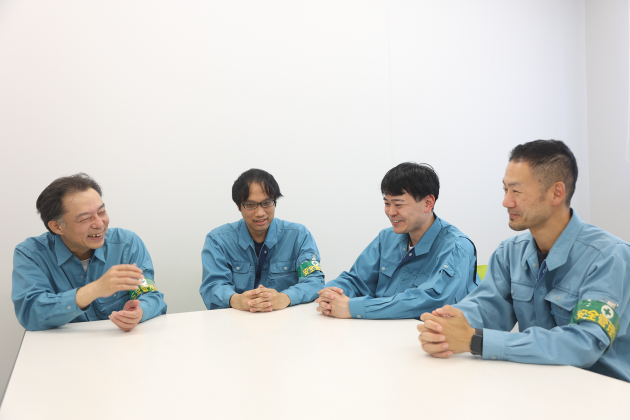
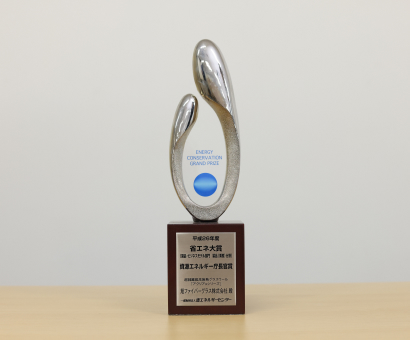
3ミクロンの、その先へ。
開発者たちの挑戦は続く。
2014年7月、ついに『Aclearα』を発売。シェアは年々拡大し、2019年には同製品の製造のために新拠点(中部工場)も立ち上がりました。ですが、リーディングカンパニーの挑戦はまだまだ続きます。
入社1年目で当プロジェクトを経験した(T.T)は、当時のことをこう振り返ります。「新人のうちから、会社の将来がかかったプロジェクトを経験できて嬉しかったですね。製品化が見えてきたという最高にモチベーションが上がる状況も体感することができ、その先につながる貴重な経験になりました」。
2014年に入ると、いよいよラストスパートが始まりました。「発売に向けて製造を本格化するとともに、第三者機関に断熱性能の測定を依頼するなど、発売直前まで慌ただしい日々が続きました。断熱性能が目標値である0.032W/(m・K)をクリアしたとの連絡が入った時には、事務所で思わず大喜びしてしまいました」(M.H)。
2014年7月に発売された『Aclearα』は、一般財団法人省エネルギーセンターが主催する平成26年度「省エネ大賞」の製品・ビジネスモデル部門において「資源エネルギー庁長官賞[製品(業務)分野]」を受賞。世界トップクラスの高性能を誇る住宅用グラスウール断熱材として、現在も日本全国で広く使用されています。
ですが、開発者たちの挑戦に終わりはありません。社内では既に、『Aclearαを超える製品開発』への挑戦がスタートを切っています。
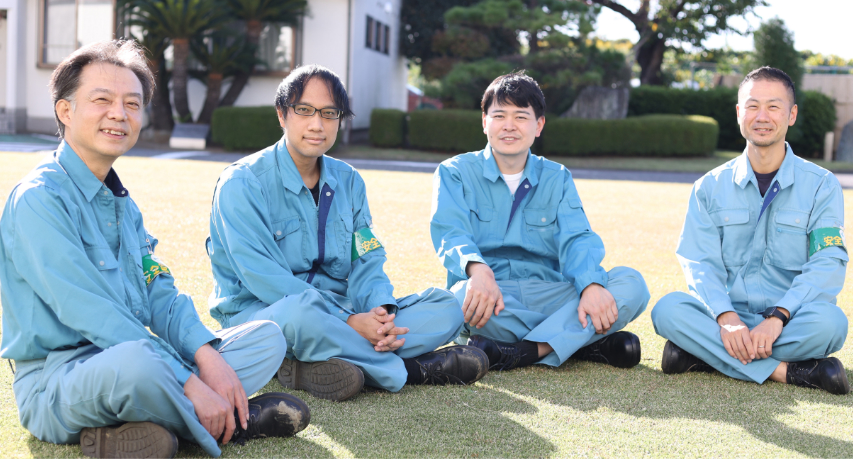